During plastic injection molding, the molten material is fed into an injection machine to be molded. After the shot is complete, the mold is pulled apart.
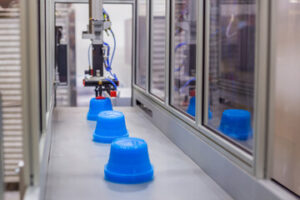
Stronger materials like steel increase the longevity of plastic molds. But, the type of plastic and injection process used will also influence the lifespan of the mold. Read on American Plastic Molds for more information.
The plastic injection molding process is a popular method for creating many different types of plastic products. The process involves heating and melting the raw plastic material into a liquid state before injecting it into the mold to form the desired product. The injected plastic is then allowed to cool before the mold is opened. The process is used for a wide variety of products including plastic cups, plates, and cooking tools. It is also commonly used to make toys and components for computers like keyboards, mice, and the outer surface of monitors and printers.
The first step in the injection molding process is to create an injection mold. The molds are made in two clamshell-style pieces that can be closed together to allow for the insertion of molten plastic. The mold base is typically made of a softer steel than the core and cavity parts to help absorb the high injection pressures. The injection machine uses a screw-like device to push the raw plastic into the mold. The screw is powered by a cylinder that helps to generate the injection pressures needed.
Once the mold has been created it is time to start making parts. The first parts are called T0 parts and serve as a test run to ensure that the mold and press parameters are working properly. T0 parts are then inspected for quality and will indicate whether any changes in the mold or press parameters need to be made before production begins. The T0 process usually takes one to two days for a small part and four or five days for larger parts.
Once the T0 parts have been inspected for quality, it is time to start producing the final plastic products. The injection process is a relatively fast one, and the cycle time can be reduced by using quick mold change systems. The cycle time is broken down into three main factors: injection time, cooling time, and ejection time. When these times can be shortened, production costs can be reduced significantly.
Extrusion Moulding
Plastic extrusion is a manufacturing technique used in many different industries and applications, from building components to food packaging. It involves forcing a hot molten plastic through a die to produce long, thin shapes with smooth surface finishes. Extrusion is a versatile, cost-effective process that can produce a range of products, from solid to hollow shapes, with high-quality results.
The process starts with a pellet or granule of plastic polymer that is fed into the main barrel of an extruder, either heated up (hot extrusion) or at room temperature (cold extrusion). As the plastic is conveyed through the barrel, it heats up to its recrystallization point and begins to melt gradually. This melted plastic is then forced through a machined metal die to create the final product. The resulting shape can be a solid, semi-hollow, or hollow profile with a smooth surface finish.
To ensure the quality of the finished product, the production process is highly controlled. The plastic is lubricated to reduce friction and to minimize the risk of a stuck-on die. A screw inside the extruder helps to keep the melted plastic moving along its path, while a heated cylinder helps to maintain a uniform temperature throughout the process.
Once the molten plastic is pushed through the die, it’s cooled down to solidify into its new form. This cooling process takes it from a hot, gooey mess to a hard-wearing, solid usable product.
While injection molding is a more precise process, it’s expensive due to the high cost of making the mold. Extrusion, on the other hand, uses less energy per unit of output and is a more environmentally conscious method of producing plastic parts. This makes it the preferred choice for companies looking to use the least amount of resources while maintaining a high level of quality control and functionality.
Rotomoulding
The steps to creating a rotomolded product vary, but in general the hollow mold is filled with powdered plastic (usually polyethylene) and heated while slowly rotating so that it melts and adheres to the walls of the mold. The rotation is important because it ensures that the resin is evenly distributed throughout the mold, which allows for a smooth and consistent finish. Then the product is cooled and allowed to harden before it can be removed from the mold.
Rotomoulding is particularly well suited for creating large and bulky, hollow products like storage bins, cases, lockers, munitions containers, industrial equipment carriers, and more. It is also a great choice for products that need to be air or water tight, such as flotation devices, tanks, and road barriers. The process can even be used to create complicated shapes with stiffening ribs and textured surfaces.
When the rotomoulding process is optimized, it offers several advantages over other plastic manufacturing processes. For example, it is less expensive to manufacture than injection molding and can produce a larger finished part. Additionally, rotomoulding is faster than other types of molding and can produce parts in one piece with no seams.
A wide variety of polymers can be molded using this method, including PET, HDPE, and LDPE. The choice of polymer depends on the type of application and on the specific needs of the customer, such as chemical resistance, strength, durability, or heat tolerance. In addition, a variety of additives can be used to optimize the manufacturing process and improve the performance of the resulting product. For example, flow modifiers can be used to improve the consistency of melted polymer, while heat stabilizers can prevent thermal degradation at high temperatures.
The rotary moulding process is relatively quick and easy, and the result is a sturdy, durable product that can be customized to fit the exact needs of the client. This process is ideal for the offshore industry, where products must be able to withstand harsh environmental conditions, such as saltwater. Moreover, it is a cost-effective and environmentally friendly way to manufacture plastic products for the offshore sector.
Cast Moulding
Cast moulding is a process that produces soft prototypes of products and components in the material intended for use. This allows the designer to rapidly test and validate the performance of a product or component in its intended environment without having to invest in expensive injection moulding die sets. It also helps speed up the design process and reduces the time to market for a new product.
The steps for creating a cast mould include preparing the pattern, constructing the mold cavity and casting the product. The mold can be made from a variety of materials such as plaster, concrete and polyurethane resin. The choice of material depends on the shape and weight of the final product as well as the casting process used.
For example, a simple cup or container is a good candidate for a one-part cast as it has no undercuts that would hinder its easy removal from the mould (as seen in the illustration below). A more complicated shape requires an open faced casting as shown in the two cups below.
A common mistake is to pour the casting into a hollowed out part of a larger object. This can result in a bubble trapped inside the mould and an uneven surface. To prevent this, it is advisable to fill the casting generously and then carefully remove any excess using a straight edge such as a plastic ruler or card. This will help to eliminate the need for any further sanding.
Another issue that can occur is air trapped in the mould. This can cause the casting to be lighter than expected or it may have an off colour appearance. To help avoid this the casting should be poured in stages, tapping and rocking as each layer is added. This should help to encourage any air bubbles to rise to the surface and escape during the pouring process.